Es standen 4 Methoden für die Modulkästen zur Auswahl:
- Den Kasten aus einem vollen Alublock fräsen. Wir haben die Methode verworfen, da wir niemanden gefunden haben, der uns die Außenseiten in RAL 7001 eloxieren konnte.
- Ein Monocoque aus Carbon zusammenkleben. Das hat sich als zu steif herausgestellt und auch nicht genug Gewicht.
- Erstellen der Module als 3D Druck. Leider haben wir keinen Drucker gefunden der 1300 x 600 x 100 mm drucken kann.
- Der Klassiker – wenig innovativ aber bewährt: einen Holzkasten aus Multiplex zusammenleimen.
Wir nehmen Multiplexholz und keine Spanplatte oder Tischlerplatte. Das Holz wird nach dem Verleimen weiß grundiert und die Seiten in RAL7001 grau lackiert.
Materialstärke:
- 12 mm für die Seiten und das Kopfprofil
- 6,5 mm für den Deckel
- 9 mm für Spanten. Die Spanten erhalten zum Deckel hin je zwei 2x2cm großen Durchlässe für Kabel. Aus optischen Gründen und um die Module auch innen gut greifen zu können, werden kreisrunde Aussparungen mit der Lochsäge eingearbeitet.
Ausgerechnet hatte ich ein Gewicht des Kastens ohne alles von ca. 7,6 kg. Gemessen habe ich mit Modulfußhaltern dann 8,2 kg.
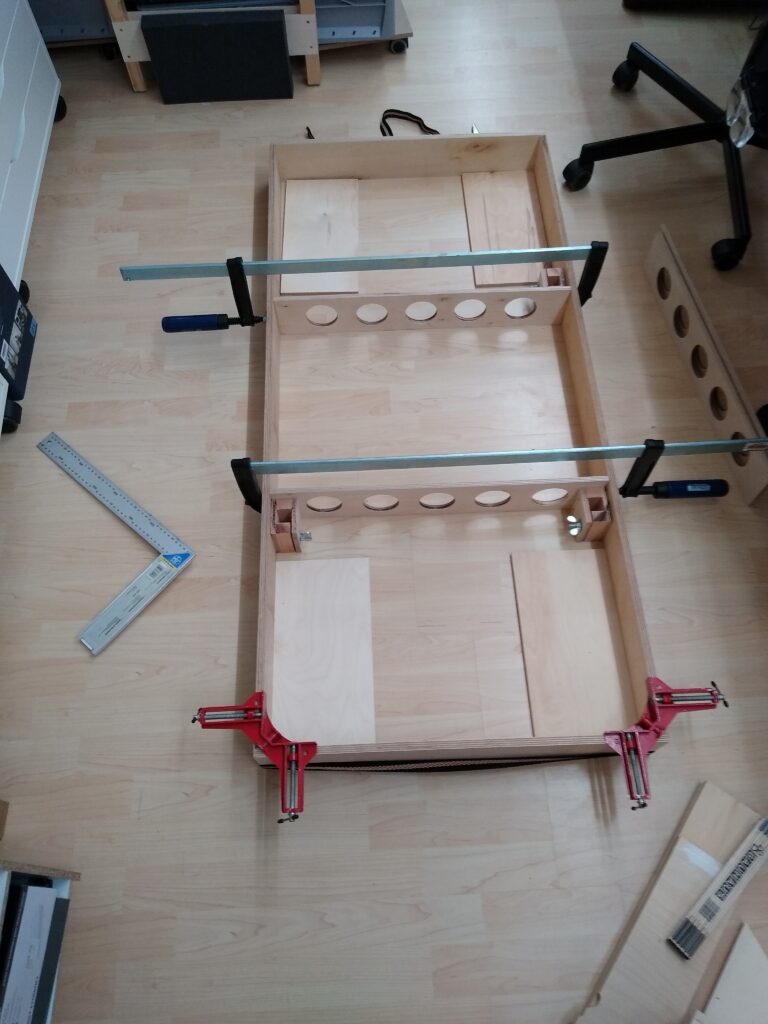
Neu ausprobiert habe ich dann die Methode, die Kanten mittels Lamellos und einer Flachdübelfräse zu verbinden. Hat prima und vor allem auch schnell funktioniert.
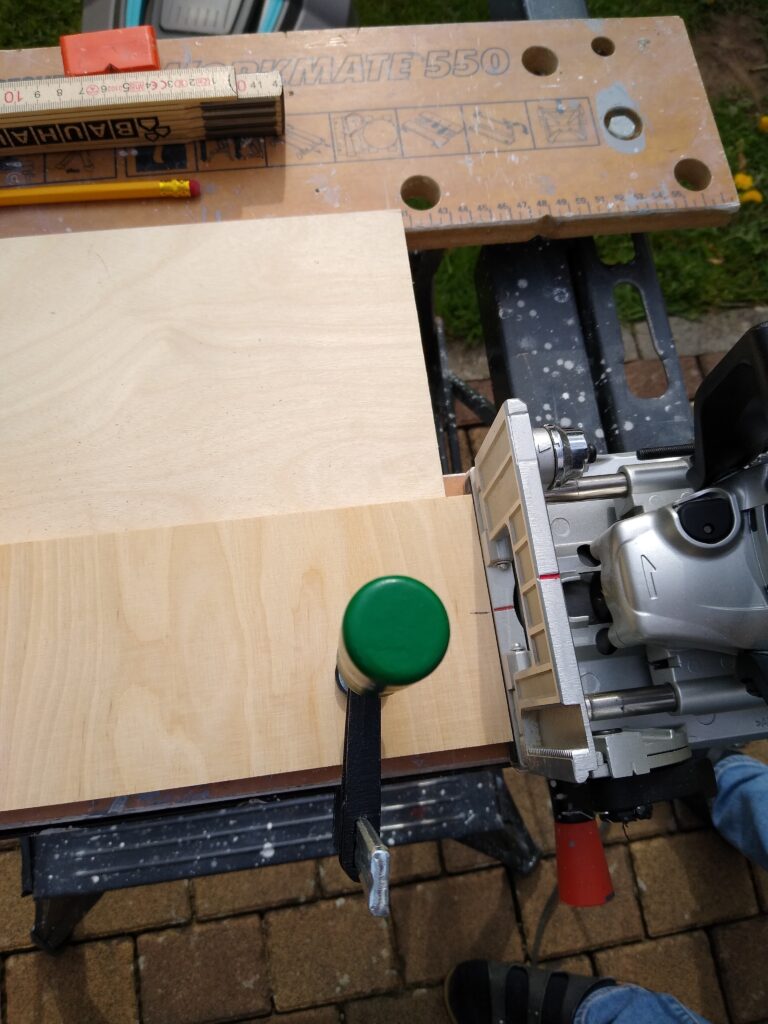
Der Deckel ist einfach aufgeleimt. Wichtig ist genügend Druck beim Aushärten des Holzleims. Dazu habe ich alle Schraubzwingen die ich im Haus hatte genutzt – die natürlich nicht ausreichten.
Den Deckel habe ich mit etwas Übermaß (1305mm) gekauft und die überstehende Kante dann sauber mit der Oberfräse glatt gezogen. Zusätzlich habe ich noch Dreiecksleisten und Winkel in die Ecken eingeleimt.
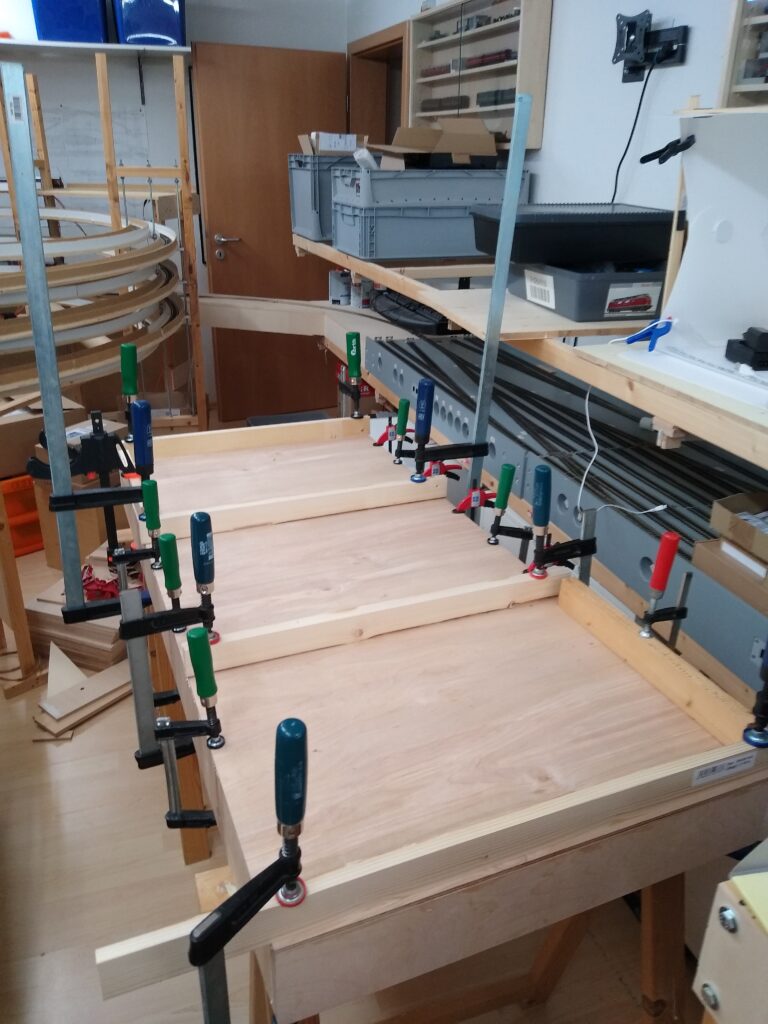
Die Kästen 2, 3, 5 und 6 sind rechtwinkelig, die Kästen 1, 4 und 7 dagegen abgeschrägt. Ursprünglich hatten wir geplant die Kästen in einer Schreinerwerkstatt über eine Bandsäge oder Kreissäge winkelig zuzuschneiden. Leider hat sich unser Plan geändert. Die Werkstatt stand kurzfristig nicht zur Verfügung.
Stattdessen bin ich wie folgt vorgegangen. Zunächst habe ich den Kasten rechtwinkelig zusammengebaut. Dort wo die Kopfbretter schräg verlaufen, habe ich dann oben und unten Querleisten von 5 cm Breite eingepasst. Beide Leisten müssen sehr präzise genau übereinander sitzen. Abgesägt wird dann mit einer Handsäge an einem Brett, dass plan zwischen den beiden Querleisten eingeschraubt wird. Zur besseren Führung der Säge ist das Brett noch mit Magneten bestückt. Das Kopfbrett wird dann stumpf aufgeleimt.
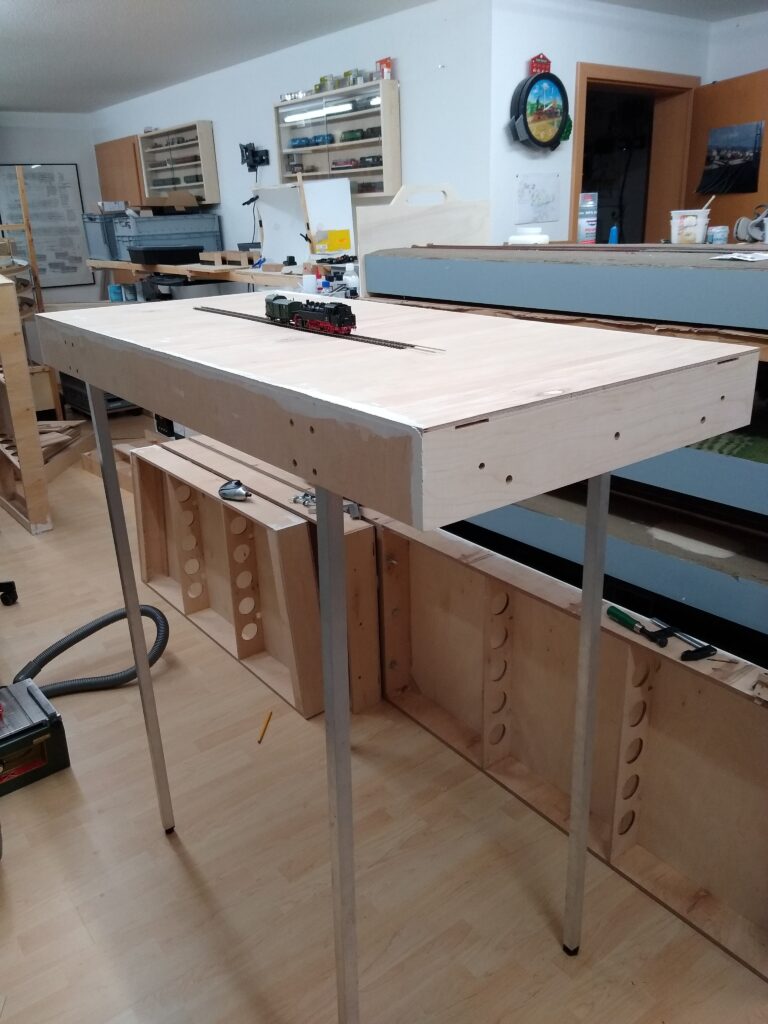
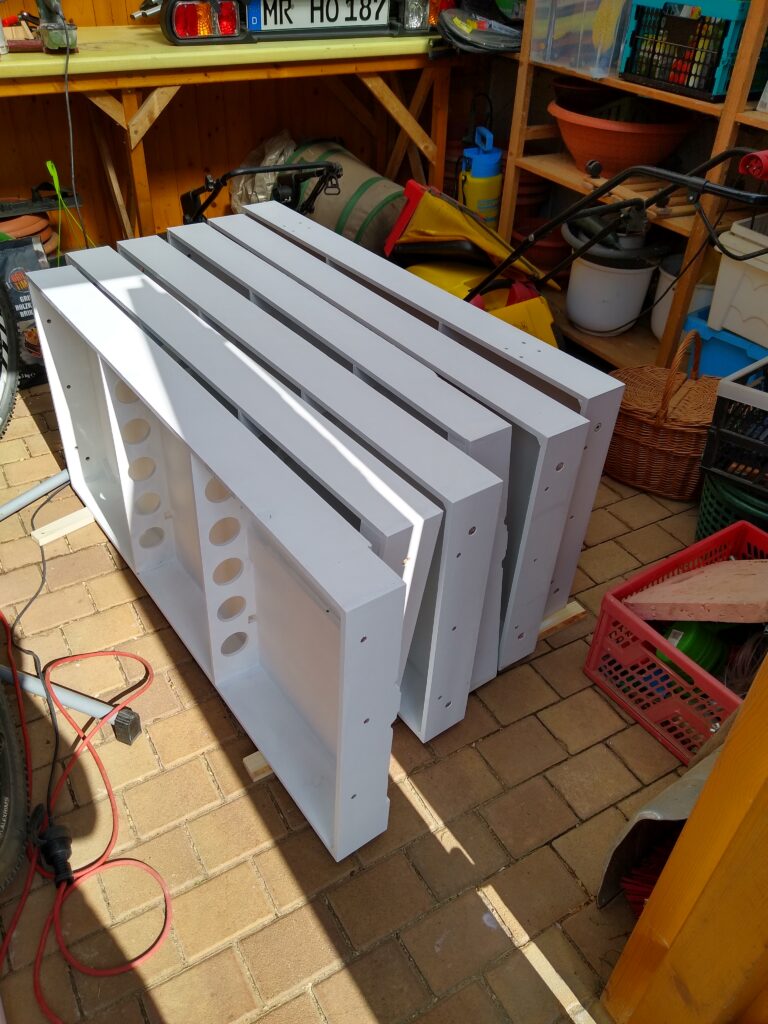
Weiter geht es mit Lackieren und Schleifen. Nur Modul 7 (Abzweig nach Lollar) muss noch nachgearbeitet werden…
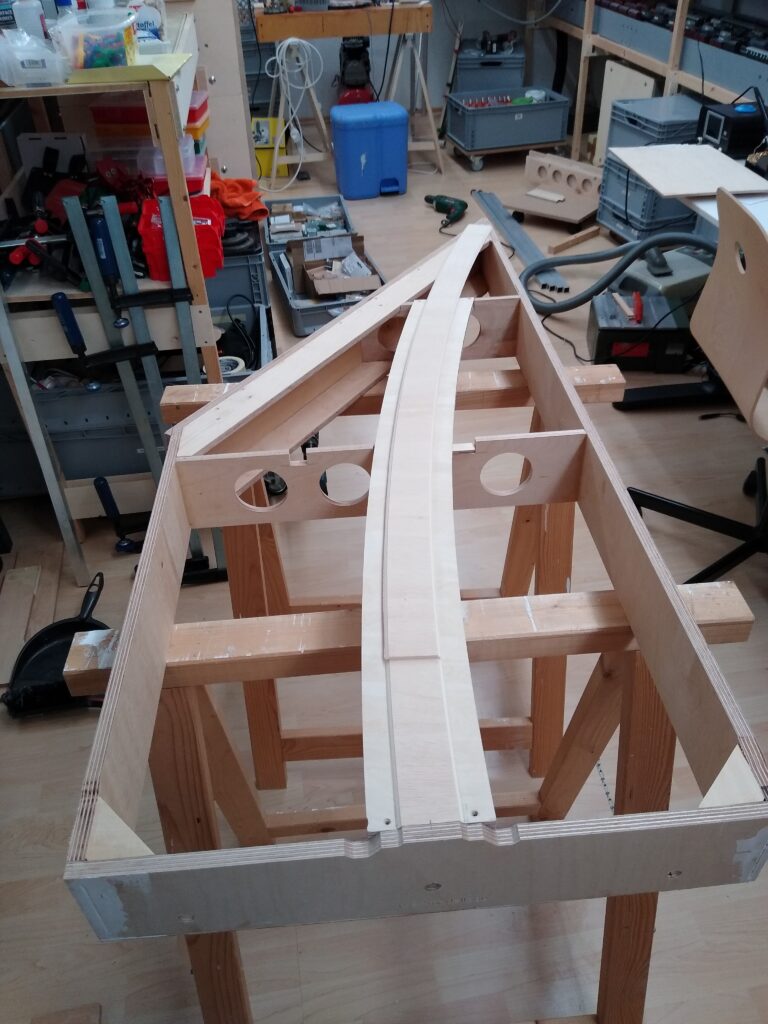
Preisfrage: Was stimmt da nicht?