Um wieder ein paar Schritte mit unserem Bahnhof weiterzukommen, haben wir uns in kleiner Runde zu einem Basteltreffen verabredet.
Wir haben uns dabei unter anderem um die Bahnsteigoberflächen gekümmert. Diese wurden mit einer Lage feinem Split versehen, um die Oberflächenstruktur der verschiedenen Teilstücke anzupassen. Auch die Böschung am Außenbahnsteig hat etwas Split abbekommen. Die Wellen in der Oberfläche sollten sich nach dem Trocknen wieder Glattziehen.
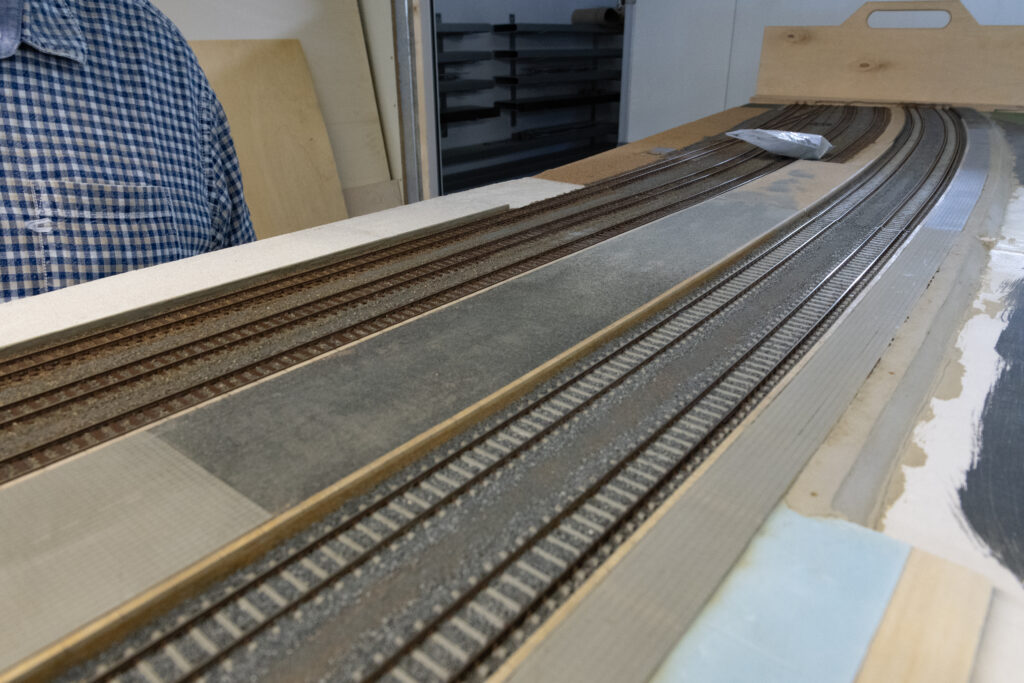
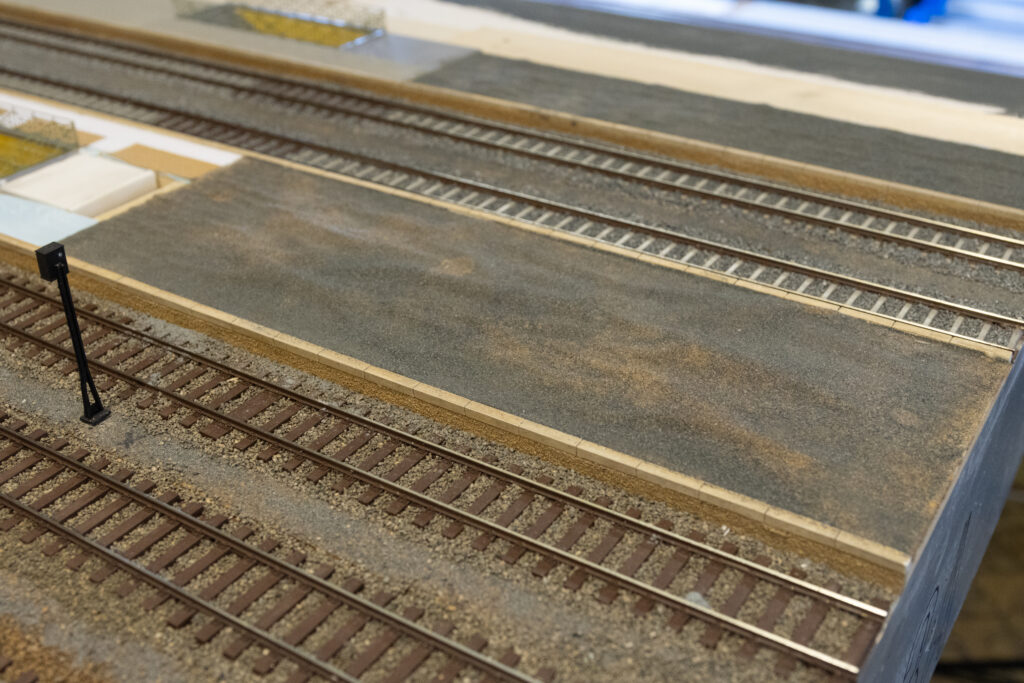
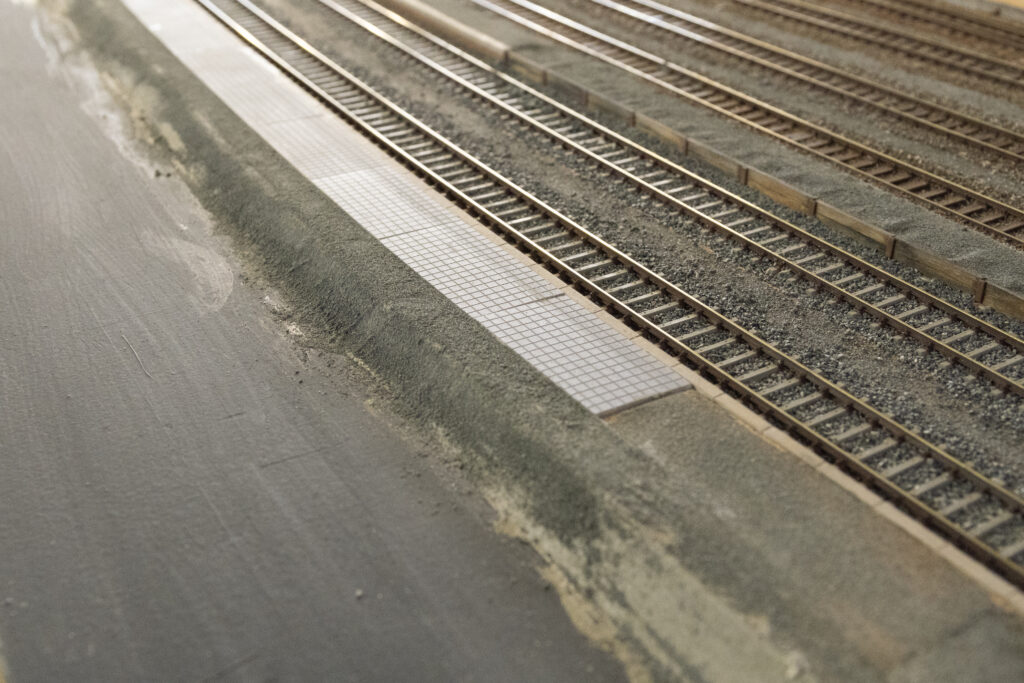
Die Arbeiten an der Bahnmeisterei sind auch sehr weit fortgeschritten. Sie hat Türen, Fenster und natürlich einen Anstrich bekommen. Das Dach wurde mit Dachpappe gedeckt und mit Schornsteinen versehen.
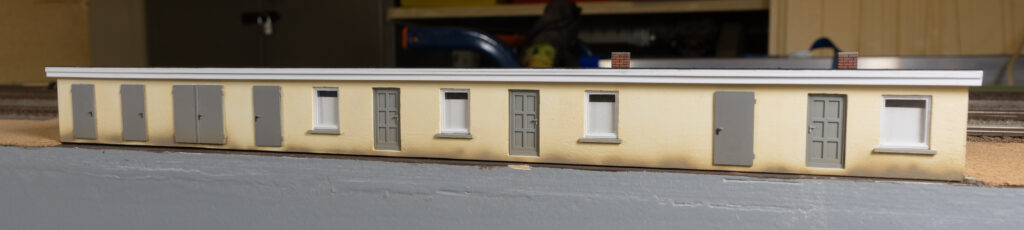
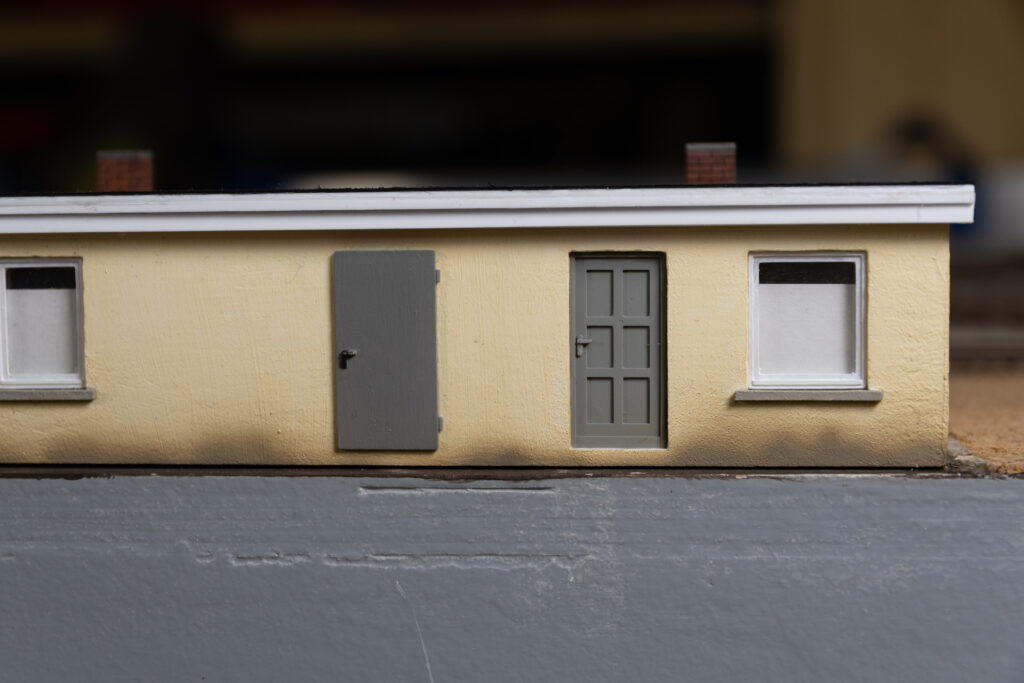
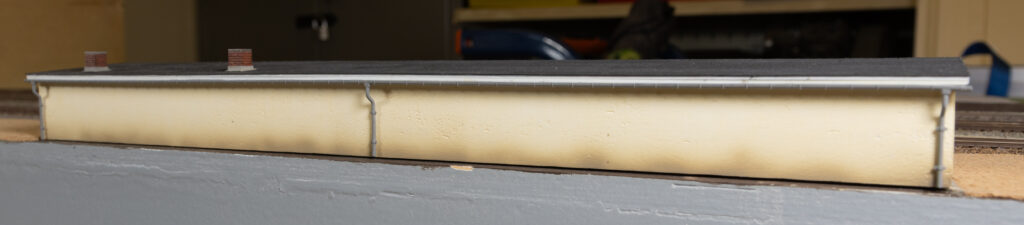
Ebenfalls etwas Farbe gab es für das Gleisfeld. Leider passte die Farbe, die wir beim letzten Basteltreffen zum Ausbessern verwendet haben, vom Farbton nicht ganz zur restlichen Farbe. Das sah auf Fotos doch sehr fleckig aus. Die ausgebesserten Stellen wurden deswegen noch einmal mit der Airbrush nachlackiert.
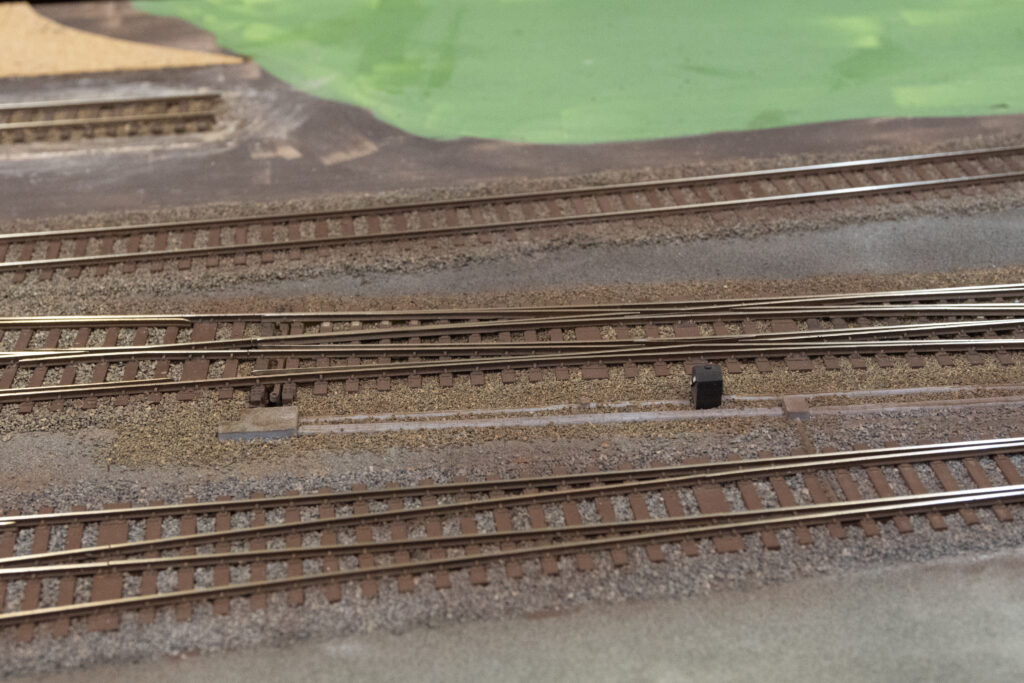
Bei der Gelegenheit bekam auch das übrige Gleisfeld noch etwas Rostfarbe ab. So wurden die unterschiedlichen Farbtöne des Schotters, des Splits und der Kabelkanäle etwas aneinander angeglichen.
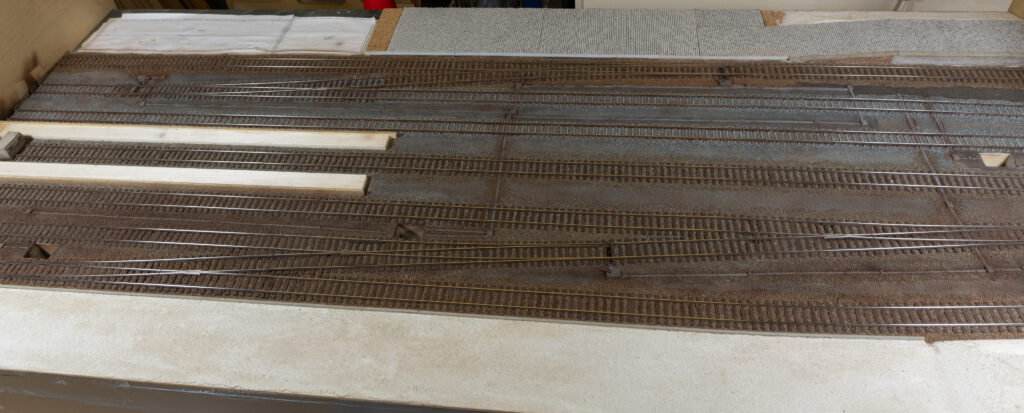
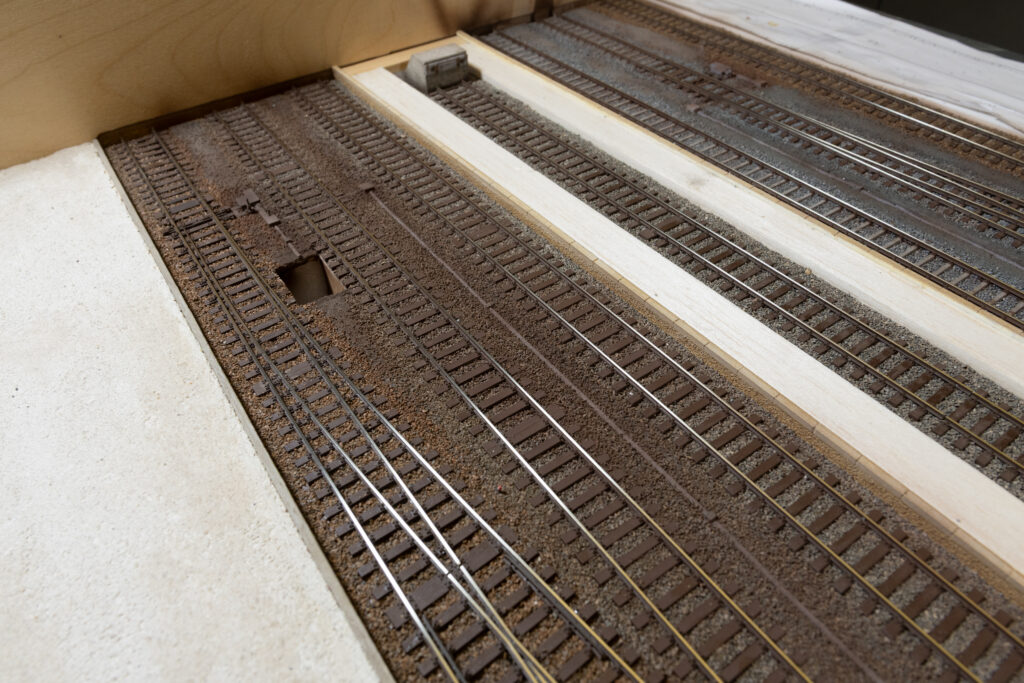
Um bei Abbau und Einpacken nicht den Überblick zu verlieren, was in welche Kiste gehört, haben wir Packlisten für jede Box erstellt.
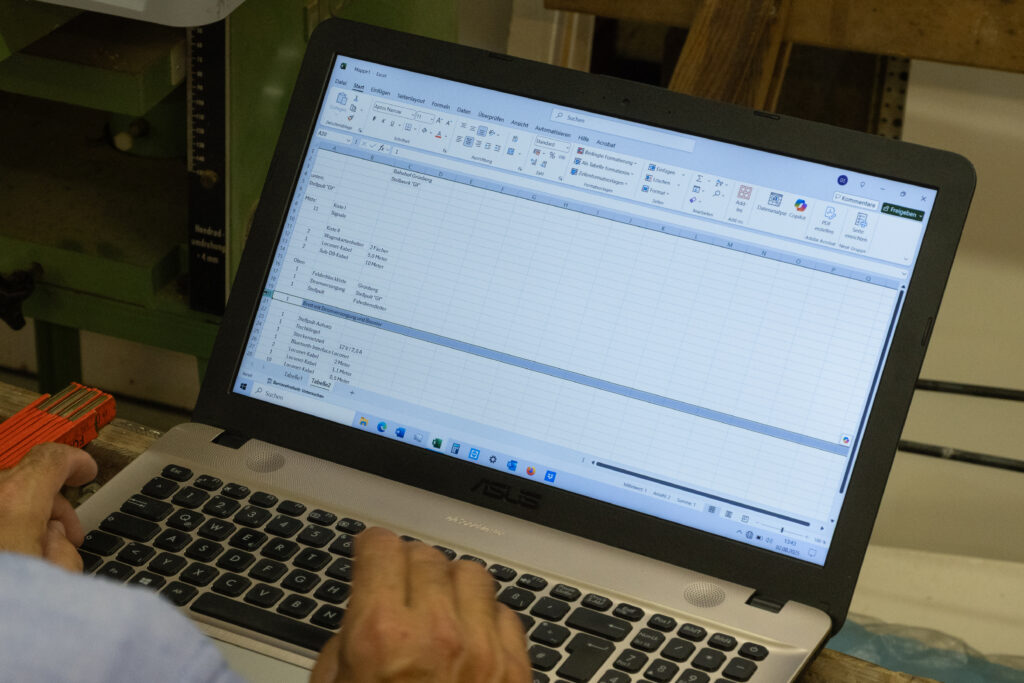
Diese werden auf die Innenseiten der Deckel der Kisten geklebt und geben so leicht sichtbar Auskunft, was sich alles in der Kiste befinden soll. Fotos vom eingeräumten Zustand helfen beim Einsortieren.
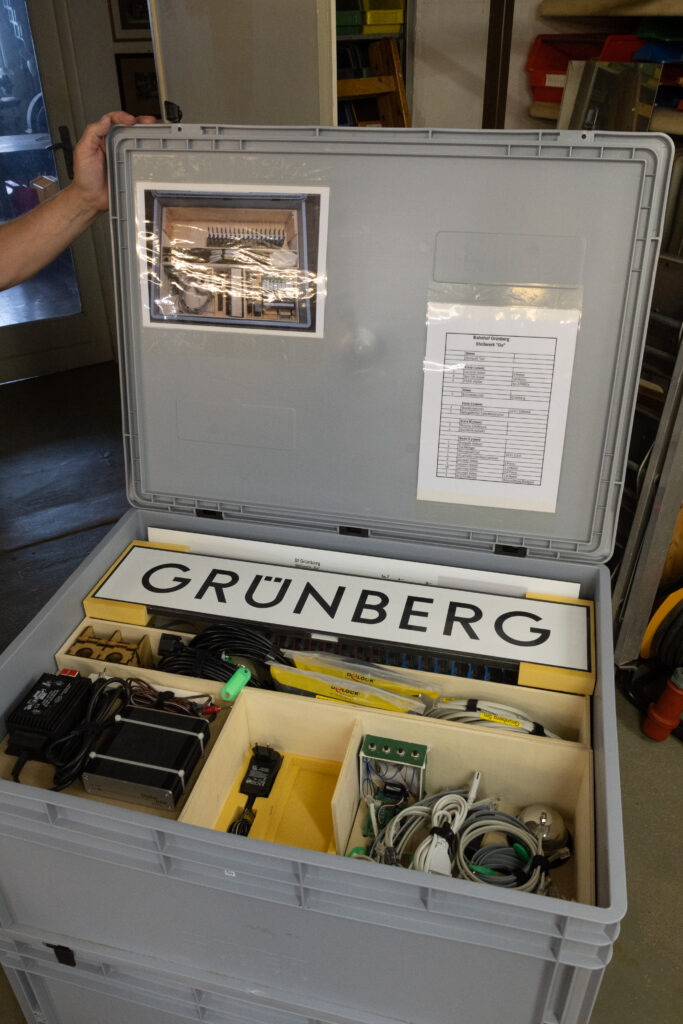
Beim letzten Basteltreffen wurden Teile der Segmente begrünt. Die loses Fasern konnten aber nicht mehr abgesaugt werden, da der Leim noch nicht vollständig abgetrocknet war. Das konnten wir dieses Mal nachholen. Wie man sieht, ist noch genug Platz für ein paar weitere Lagen Fasern:-)
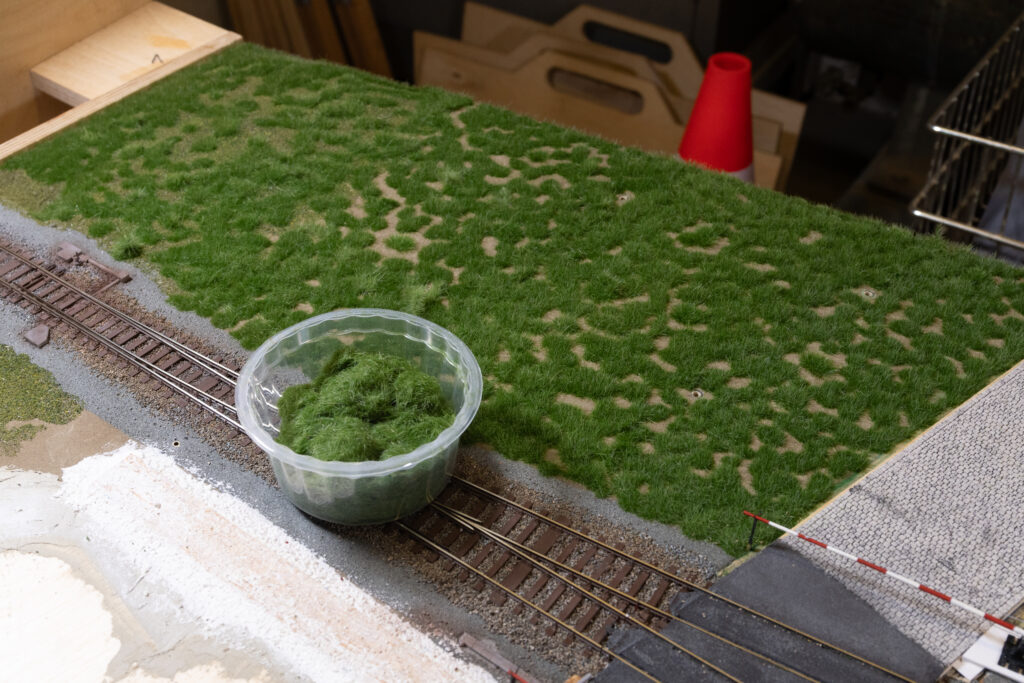
Im Bahnhof Grünberg gab es einen einzigen Wasserkran, der in der Nähe des Stellwerks Gf aufgestellt war, da sich dort der Hochbehälter mit dem Wasser befand. Mit einer Stellprobe haben wir die zukünftige Position des Wasserkrans bestimmt. Nach Vorbildfotos wissen wir, dass er genau im Zwickel der Einfahrtweiche stand, so dass die wasserfassenden Loks zeitweise die nächste Weiche blockierten. Die kurzen Rohrleitungen scheinen damals bei der Festlegung der Position wichtiger gewesen zu sein als ein ungehinderter Betrieb.

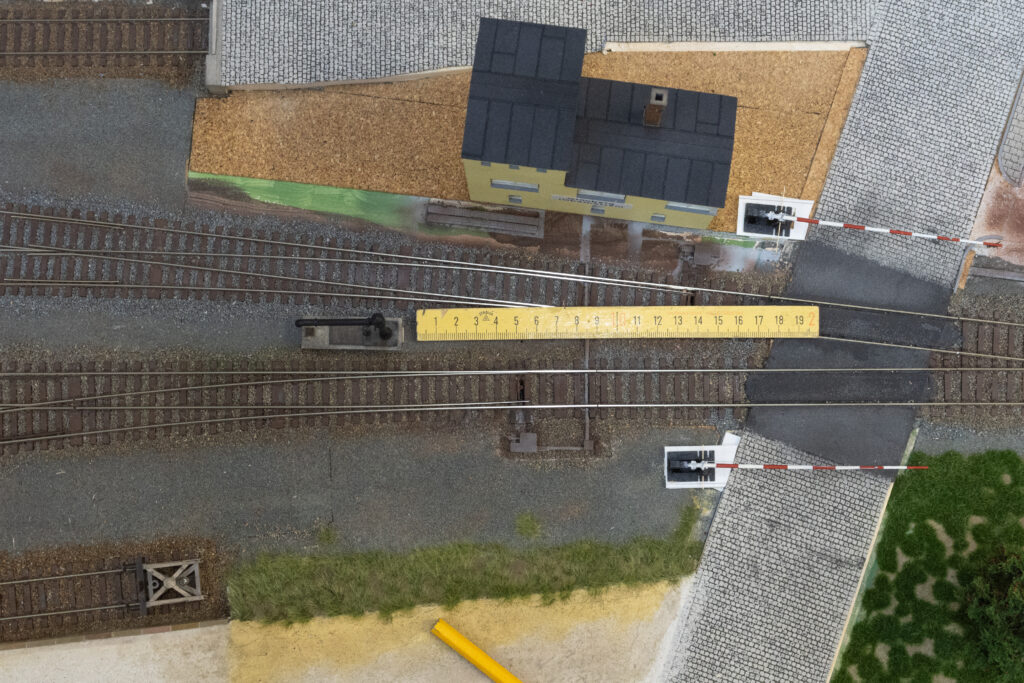